Custom Medical Cable & Wire Manufacturing by a Leading Medical Cable Manufacturer
Medical devices and equipment are critical to saving lives and ensuring safety. As a key part of medical interconnect solutions, medical cable manufacturing plays a crucial role in healthcare.
We are a leading medical cable expert, specializing in the design and manufacture of a wide range of custom medical cables and wires for medical equipment factories and medical accessories manufacturers. From design and prototyping to testing and mass production, we can complete custom cable projects in just 7-10 working days, charging only for material costs (with free design consultation and existing samples available).
Our Regular Medical cables manufuring service
With over 20 years of experience serving medical cable assembly manufacturers and medical device manufacturers, we have produced thousands of cables. Our specialty lies in manufacturing medical accessories cables for ICU monitoring systems and first aid systems. We also offer regular stock of cables with standardized specifications, allowing multiple accessories manufacturers to share the same cable and providing the lowest cost, highest productivity, and safest operations.
Choose us as your trusted partner for high-quality custom medical cables and wire manufacturing.
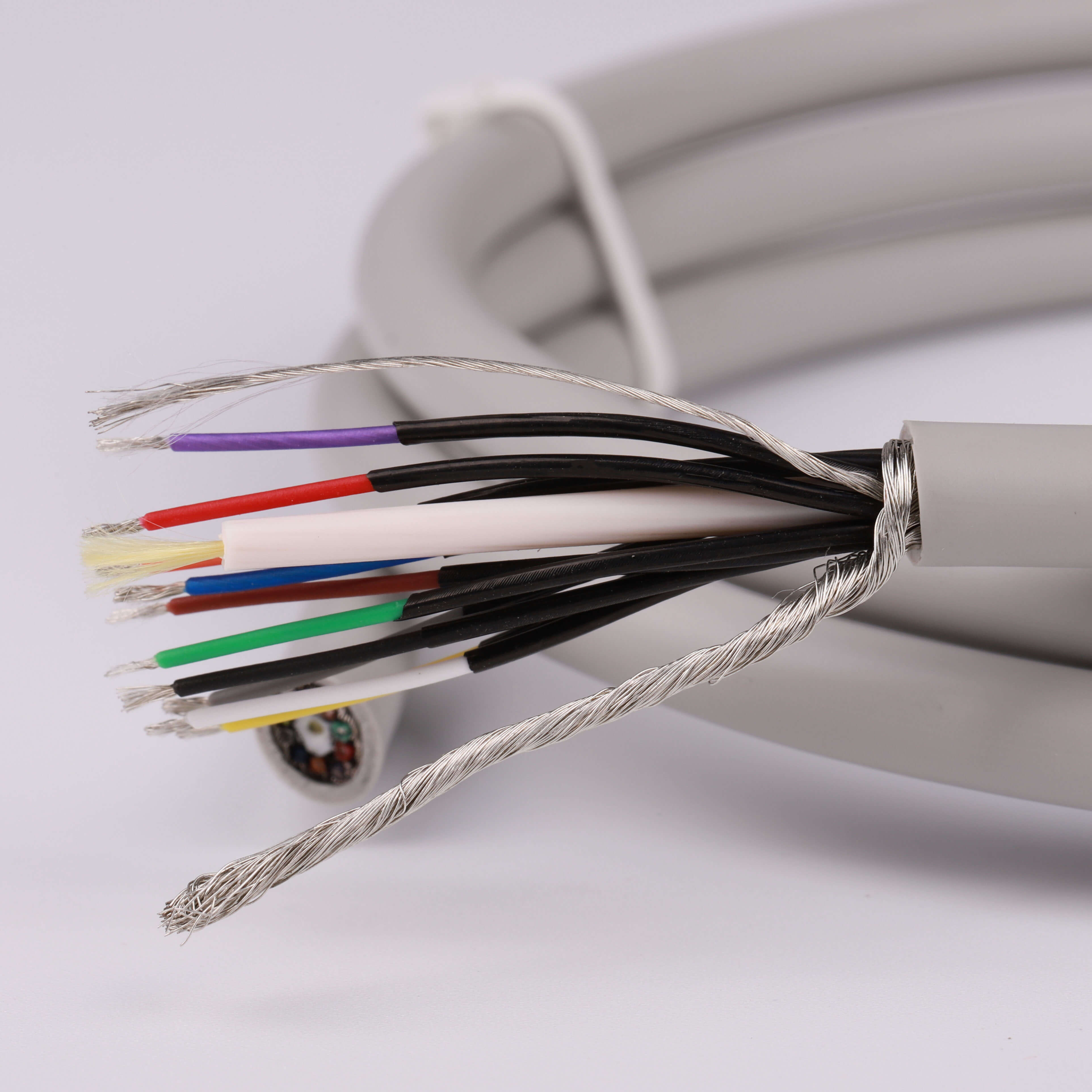
ECG Cable
single leads to 18 leads ECG trunk cable and one-piece series ECG lead wire
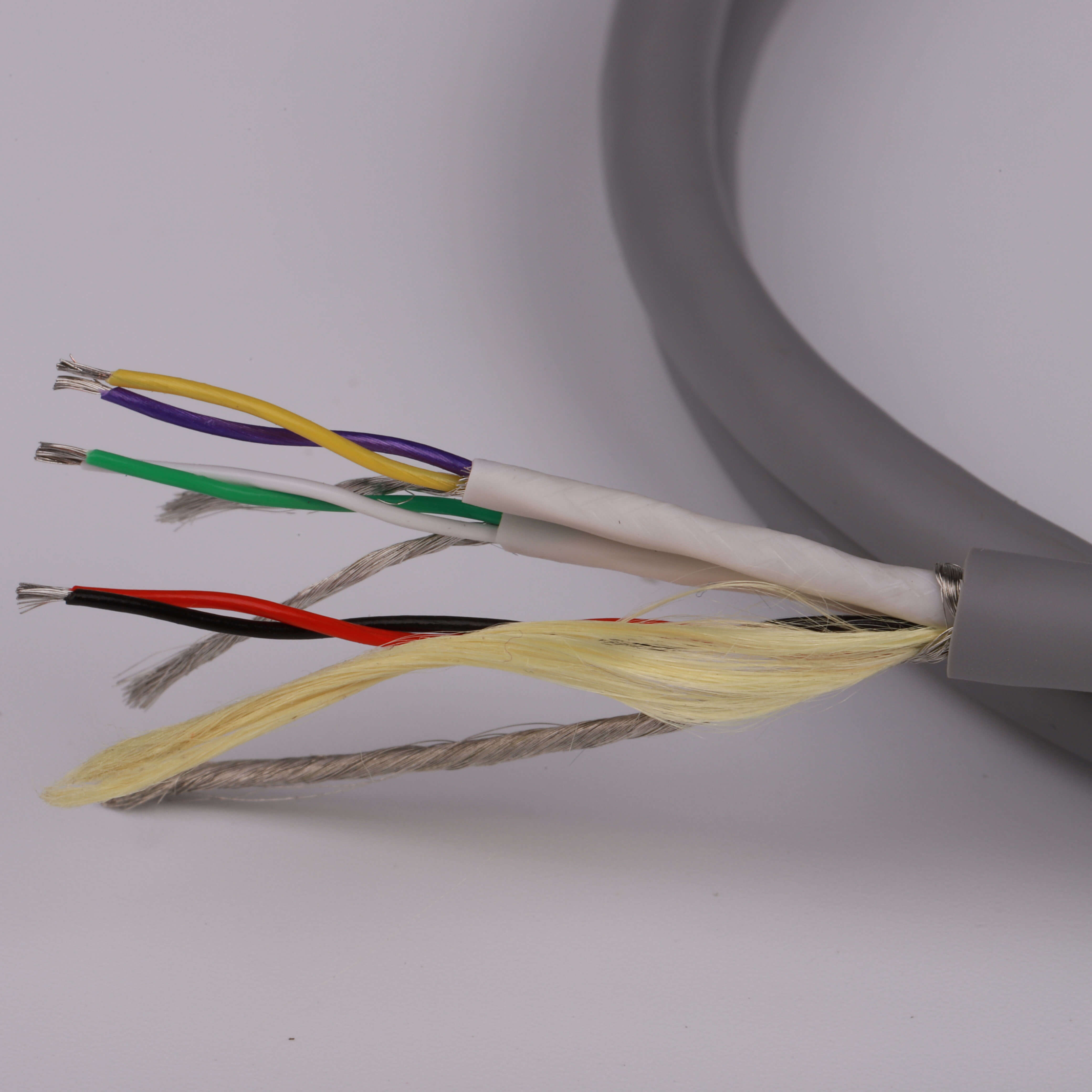
Spo2 cables
Disposable and Resusable Spo2 cable in round or flat ribbon cable
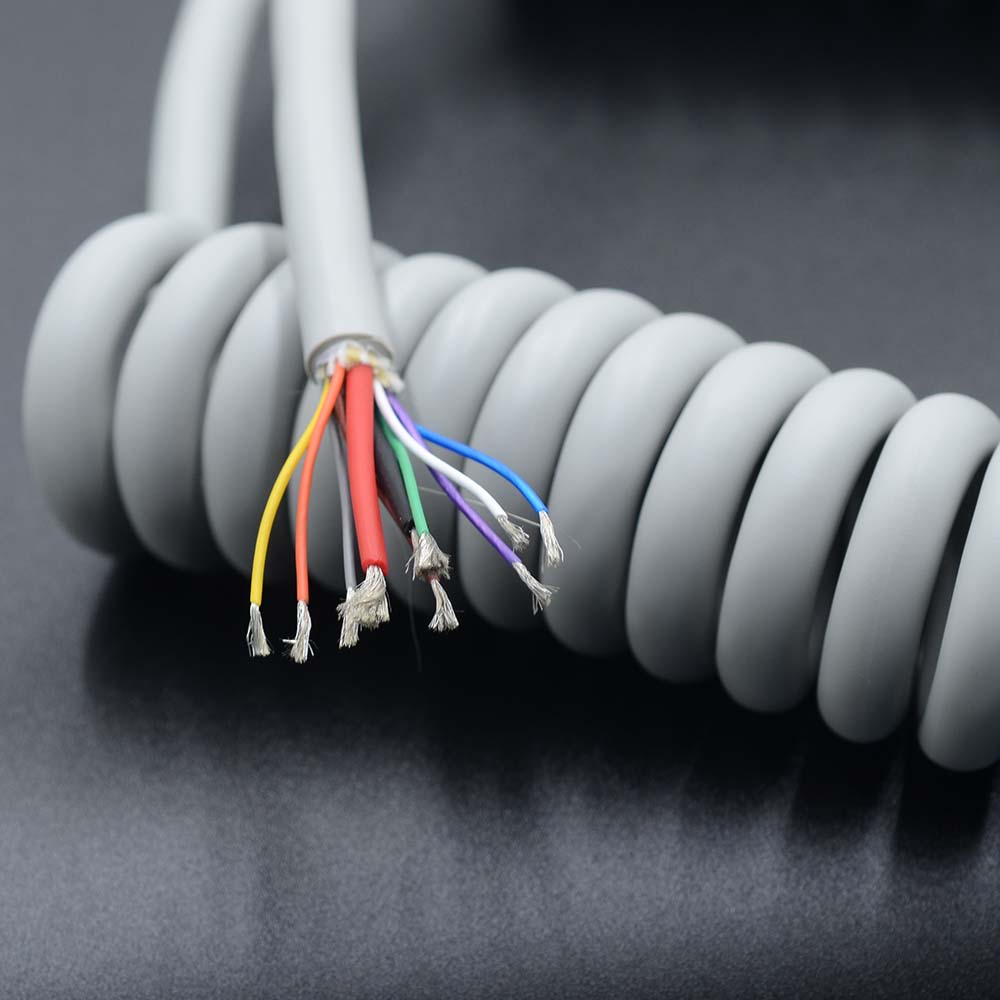
Defibrillator cable
Defibrilltor cable Coiled &Defibrillator leads&Pacing leads Flat Ribbon
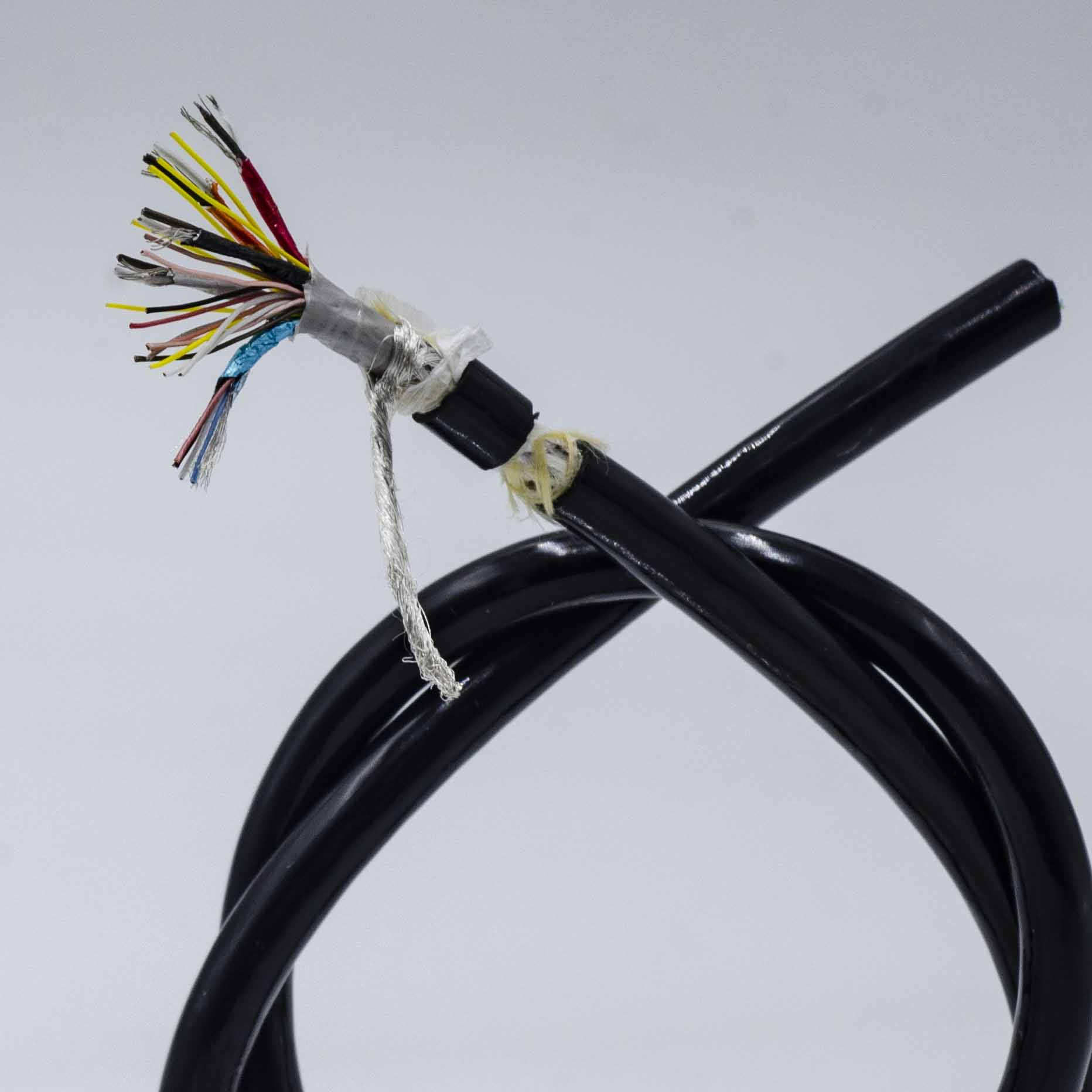
endoscope cable
endoscope cable and borescope cable with miniature coaxial cable
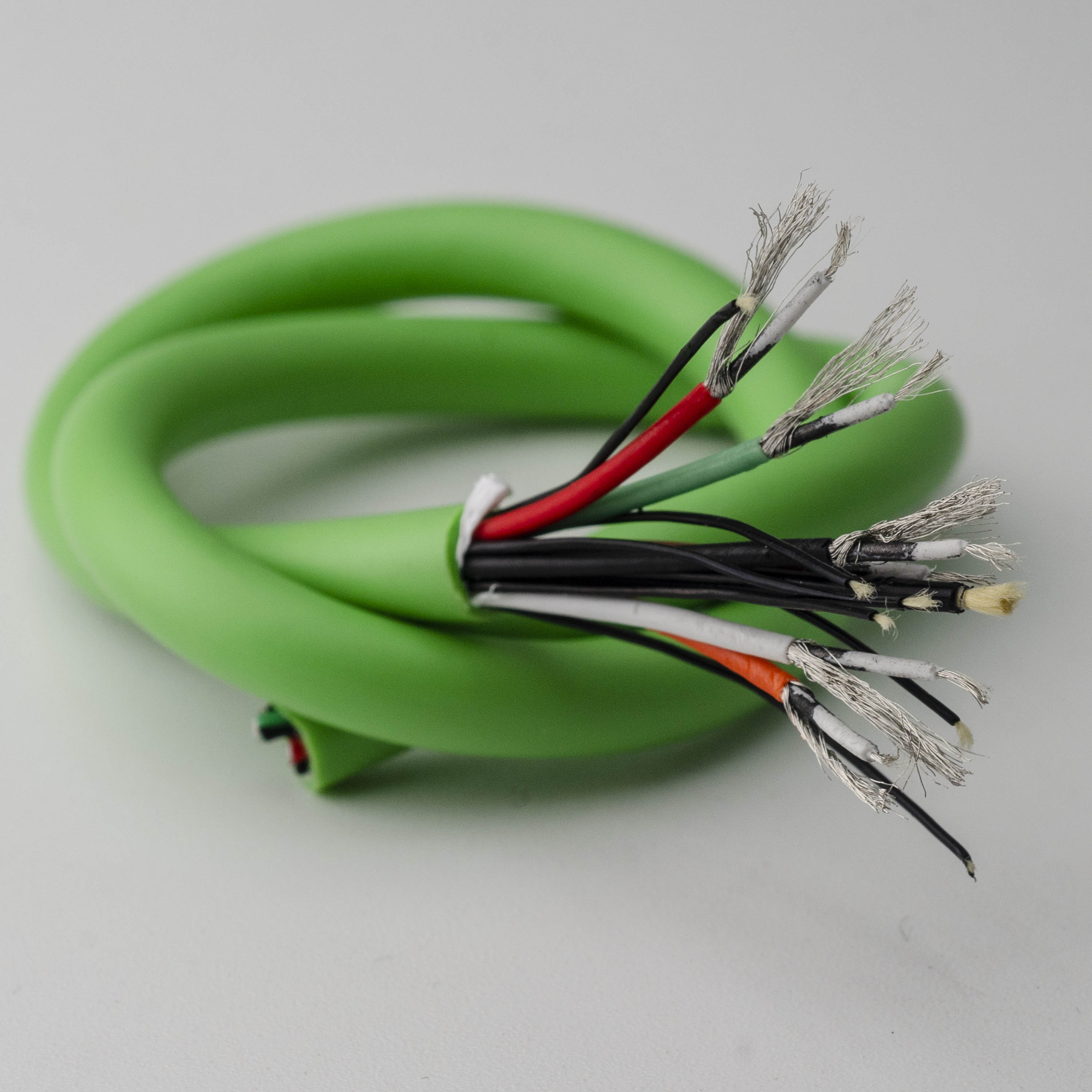
Low Noise Cable
Low Noise cable with Graphene coating and conductive low noise layer
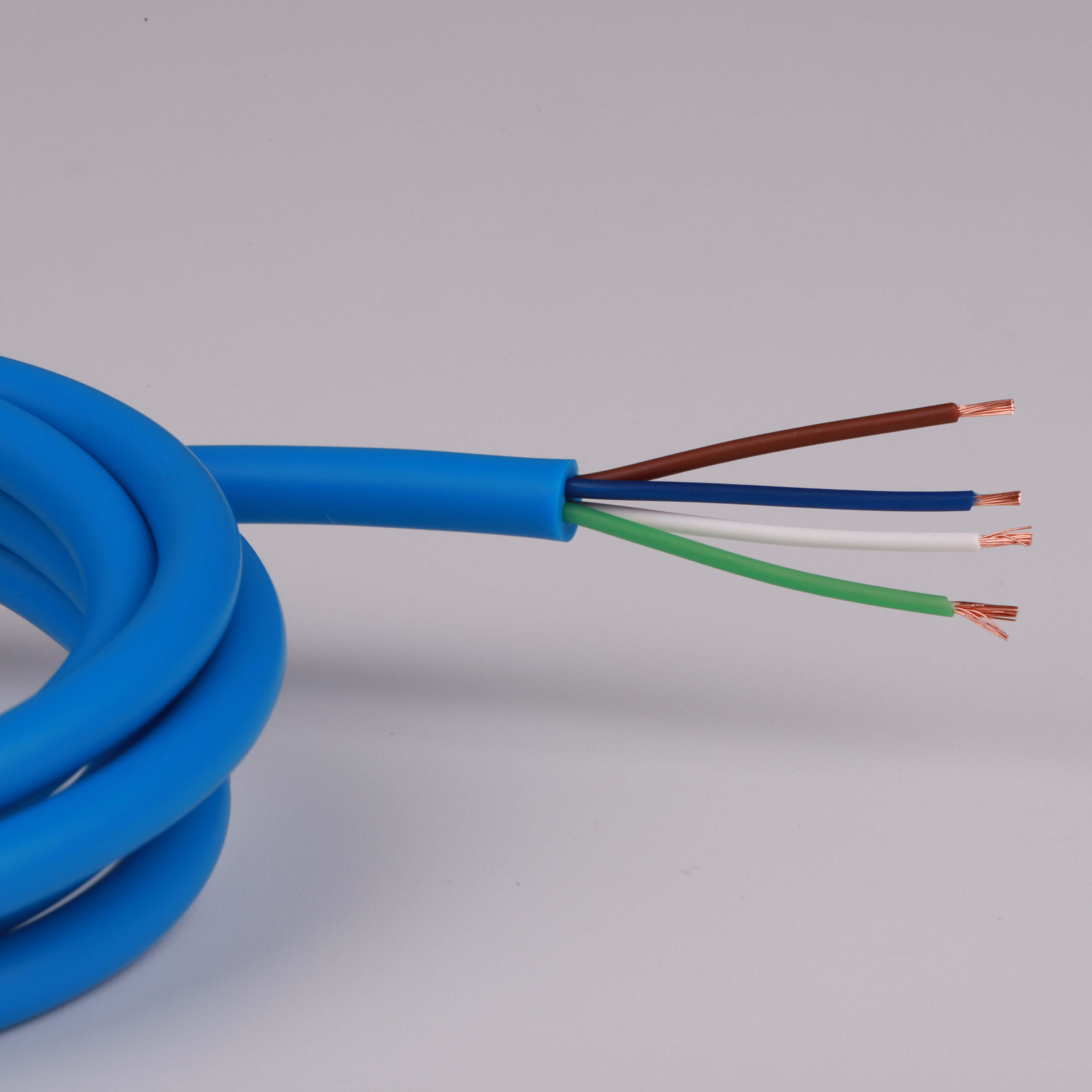
ESU Cable
3 core or 4 core Disposable ESU cable and Silicone resualbe ESU calbe
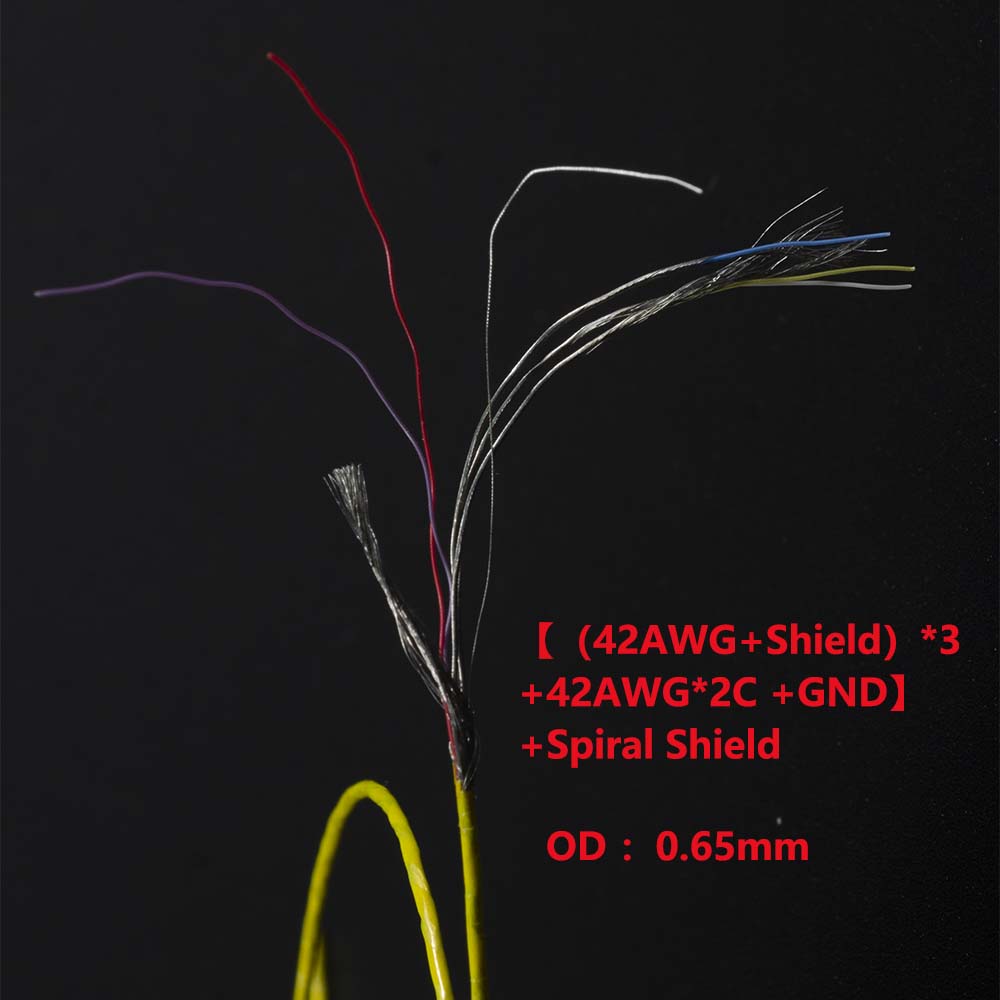
Endoscope Camera Cable
For Camera OVM 2740 6946 6948 6949 9734/ TA10/ FA10/OCHSA10/ES101

Xray Cable
High Voltage Cable
75KV/90KV Option
Straight and Rectangle
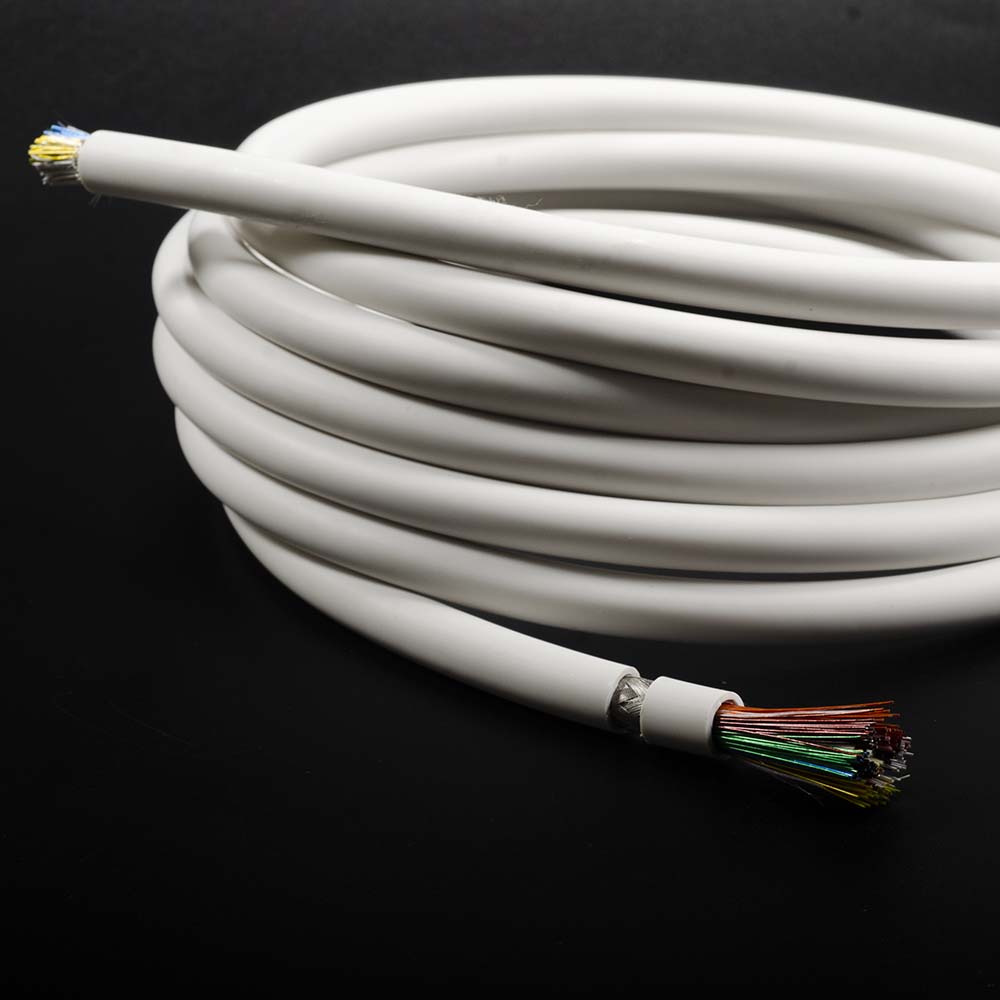
Ultrasound Probe Cable
Custom 44AWG-42AWG Physical foamed Low Capacity 50PF-60PF
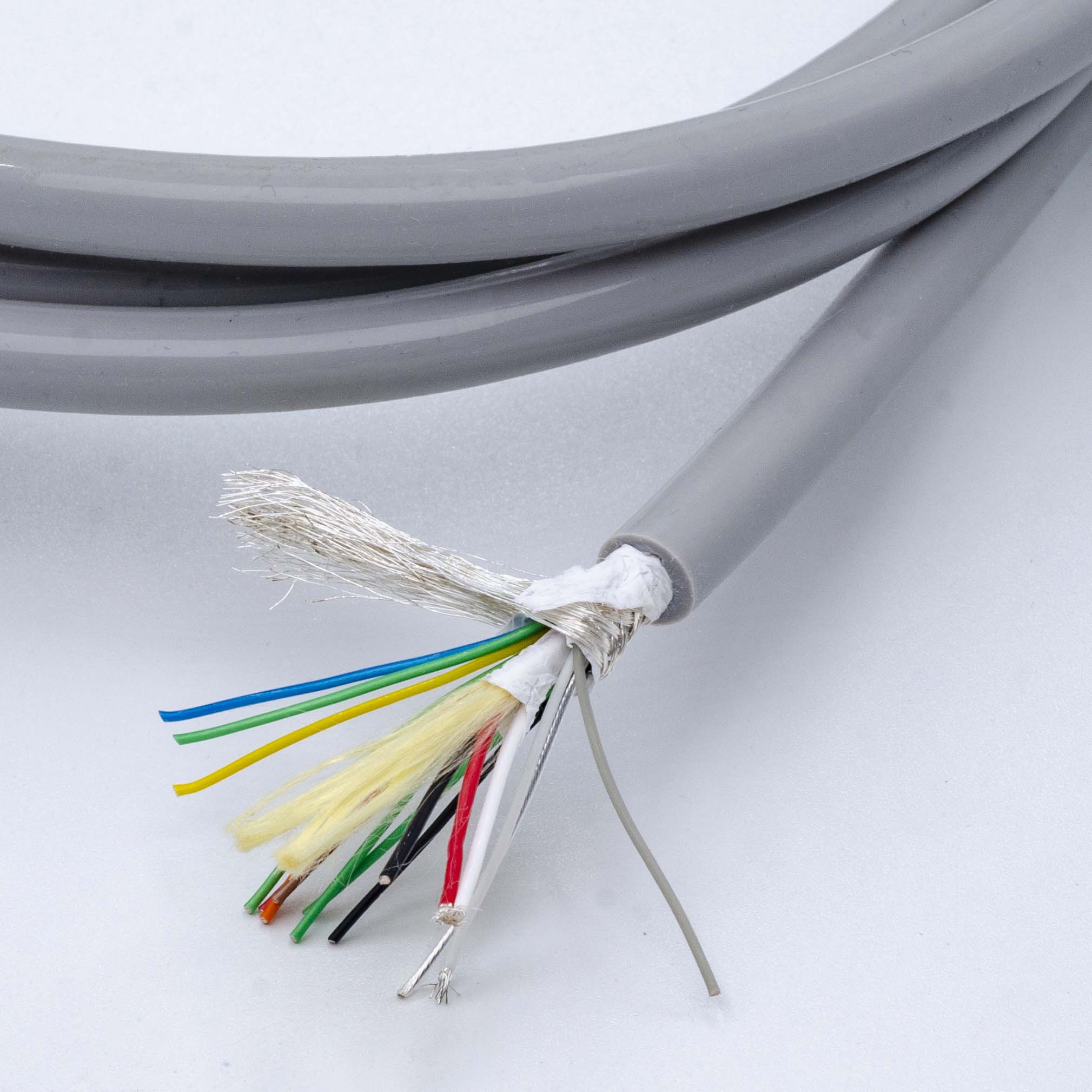
Silicone cable
Silicone cable with teflon wire for hard envrionment,Small diameter for high voltage
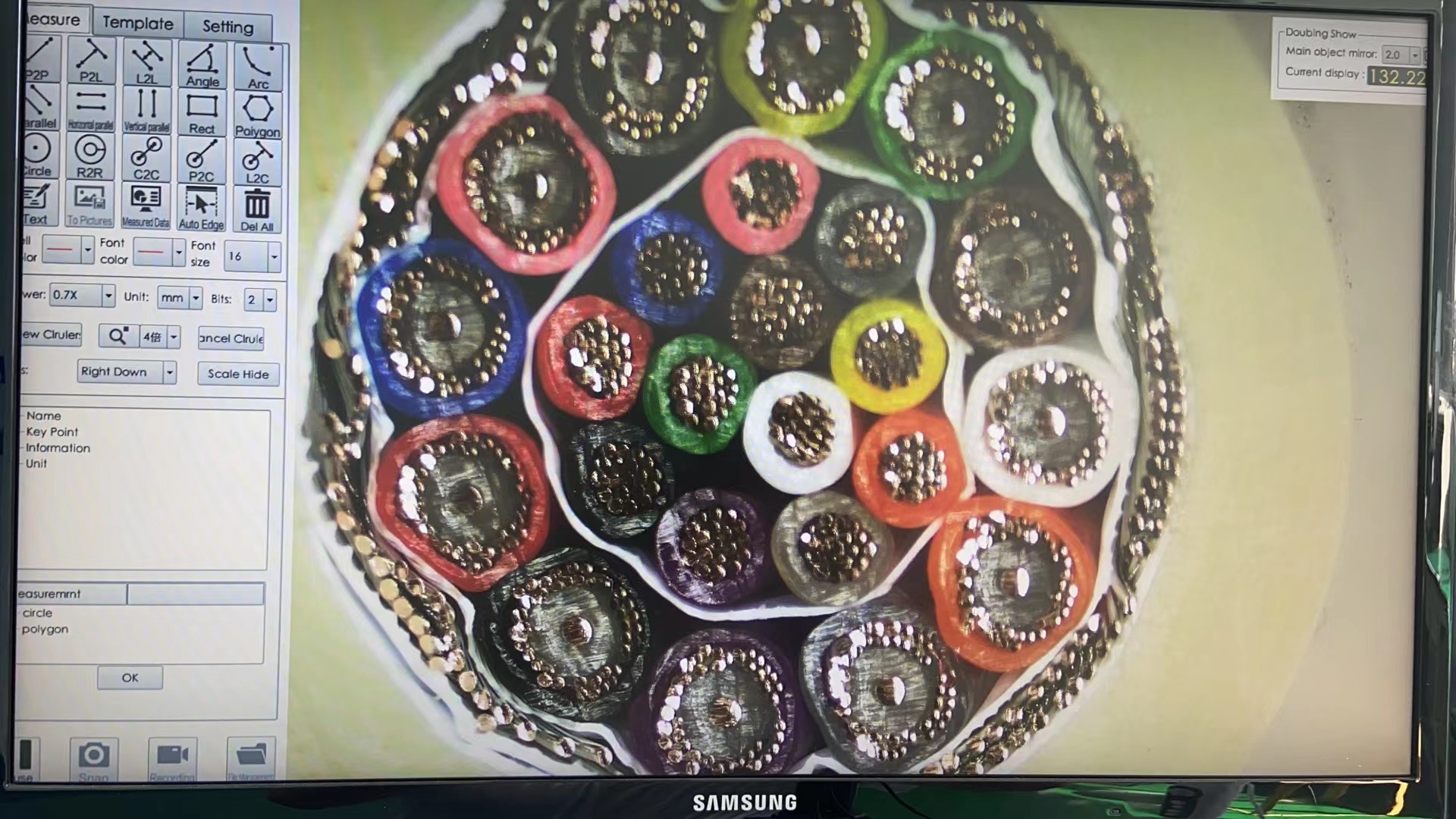
MRI Cable
Non-Magnetic,Non-Ferrous,Non-H+Proton Interference,Low Capacitance,Low VSWR,Low Attenuation,Custom manufacture
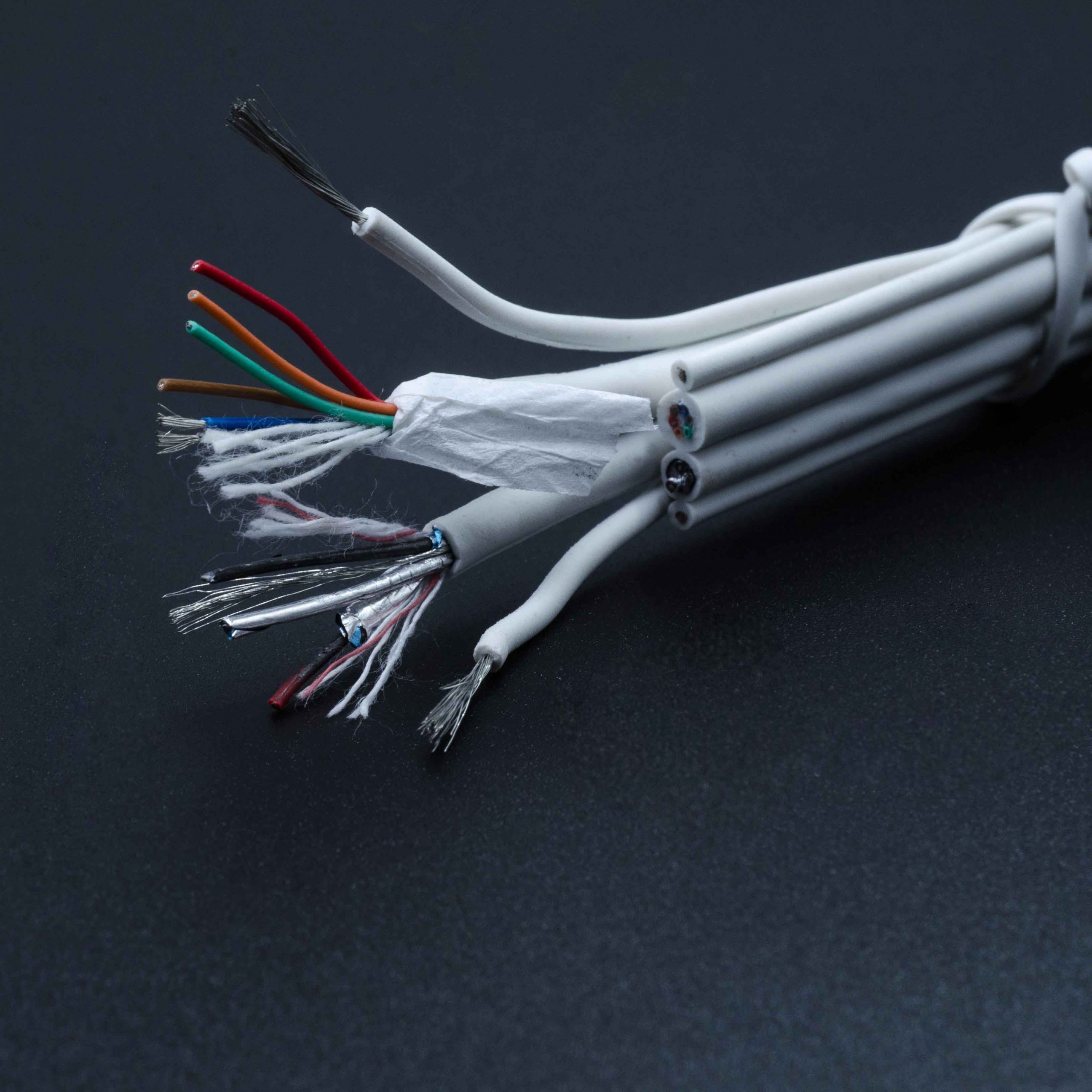
bundled cable
Custom bundled cable includes wire ,fiber,tube,kevlar...
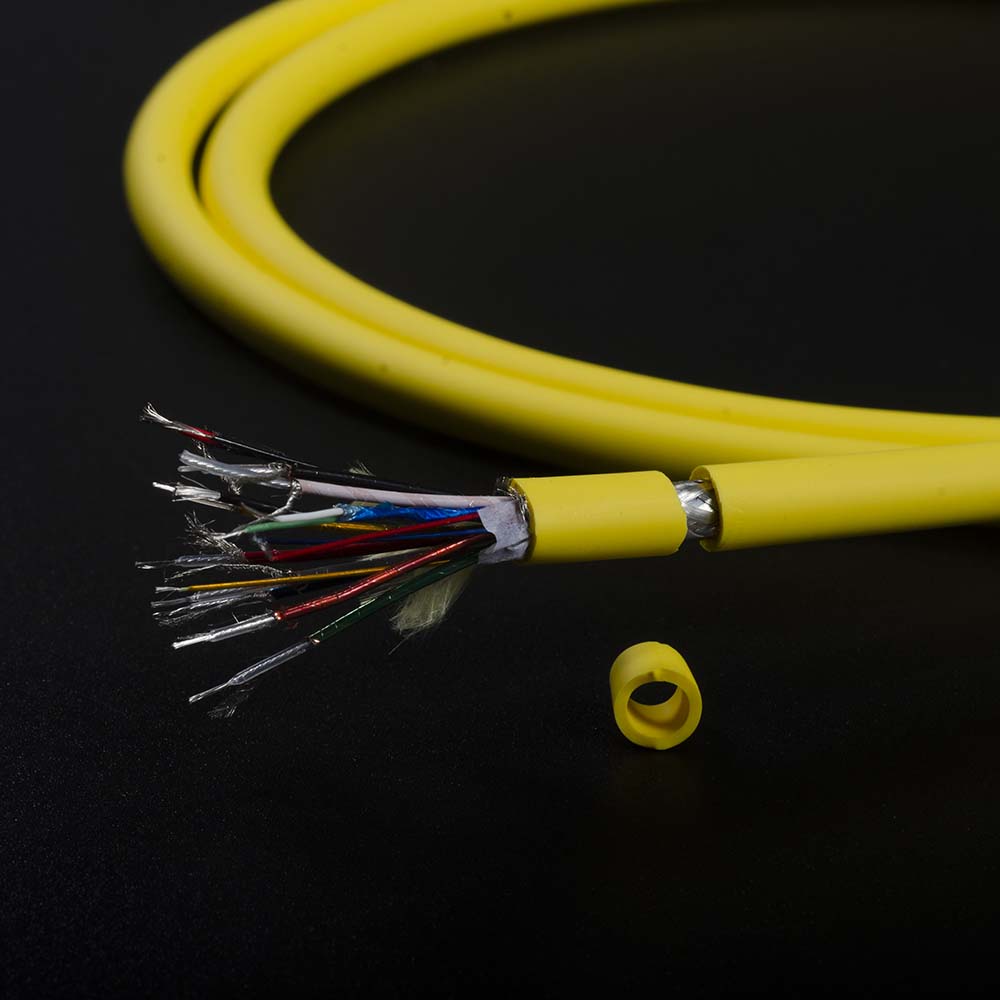
USB Bulk Cable
Medical Grade and Commercial level USB3.0,USB3.1 and USB 3.2 cable,High Speed,Low Lose ,Small Diameter
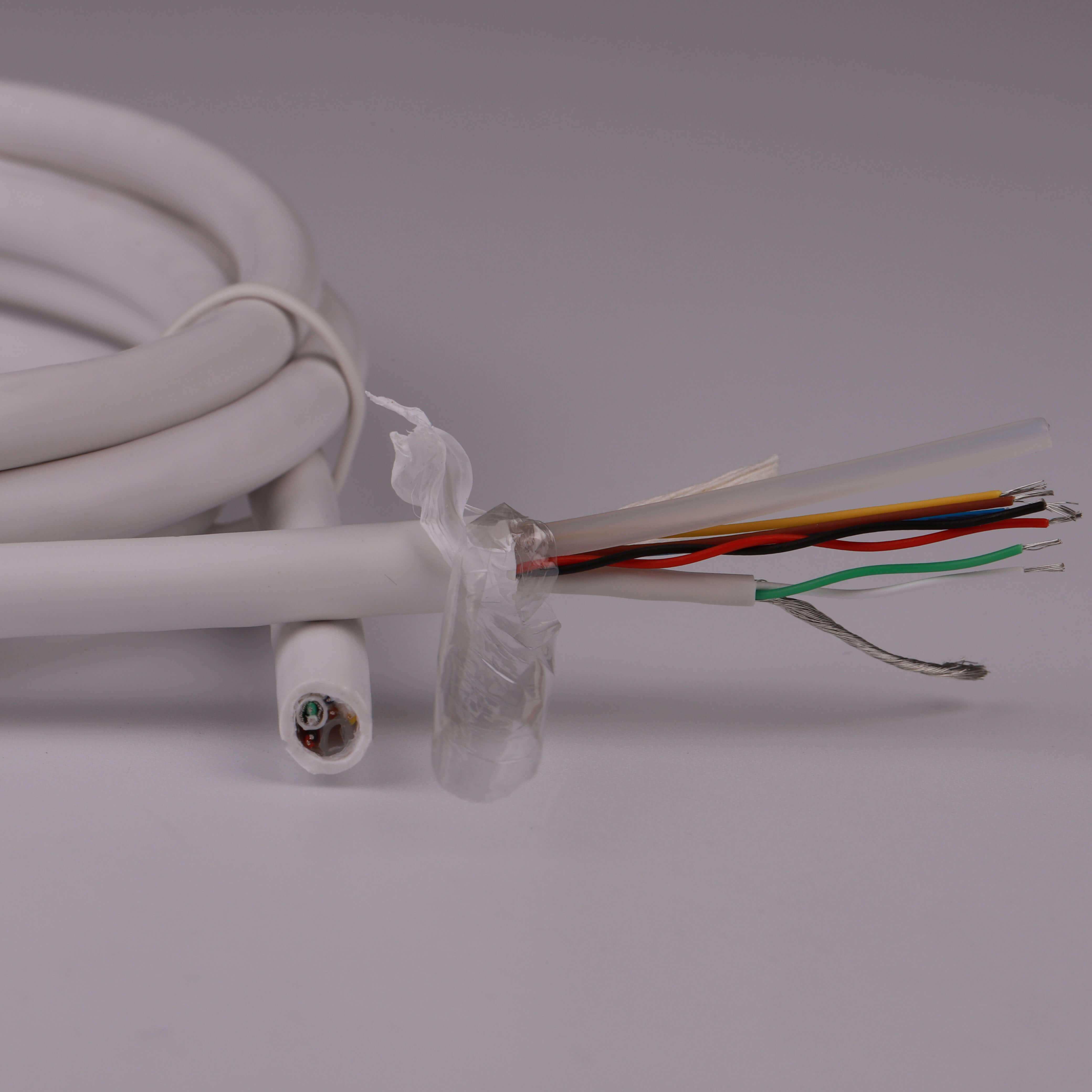
Medical tubing Hose
custom Medical cable with airpipe ,NIBP Hose,NIBP tubing
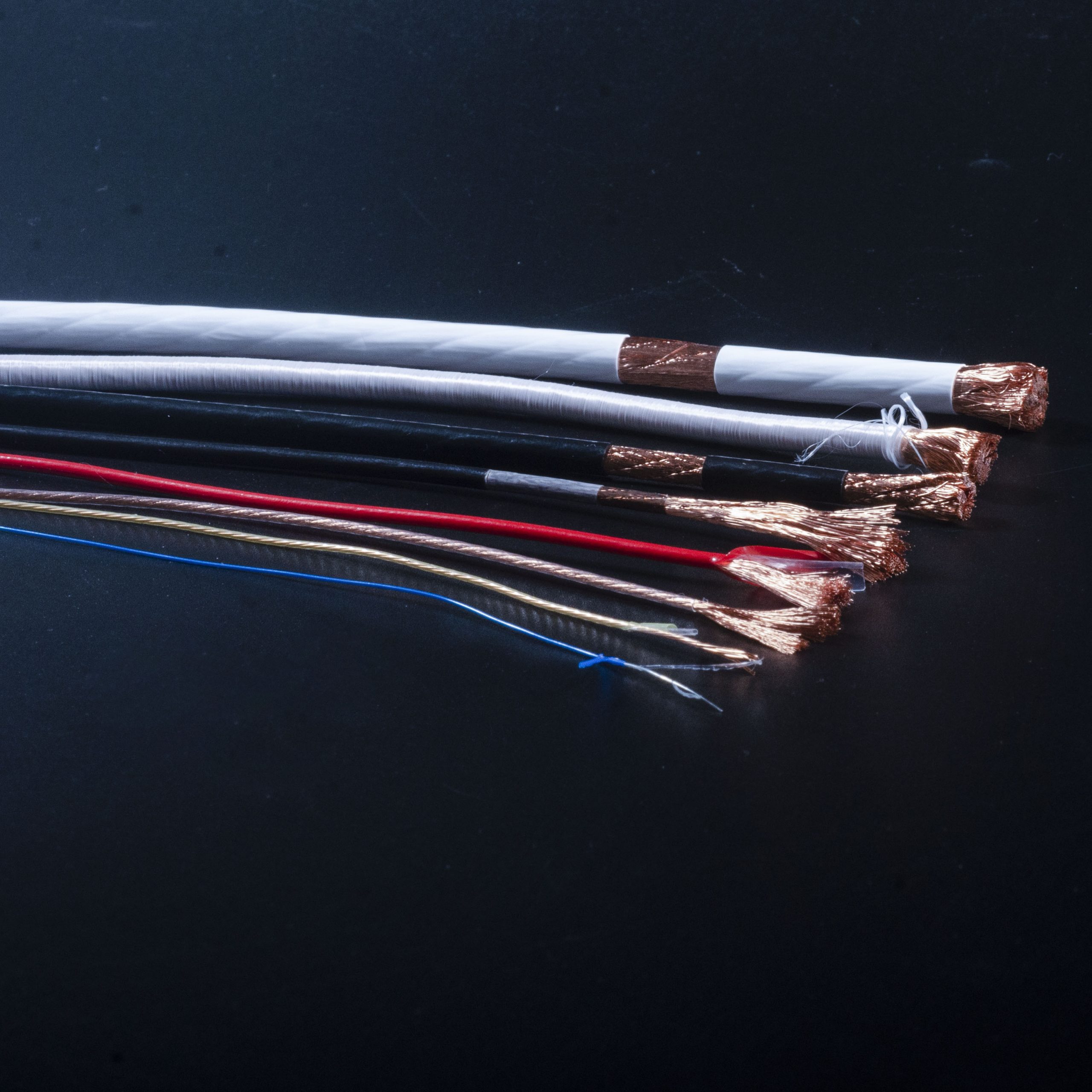
Litz Wire
Different Litz wire types for option.Type 1 to type 6 are round, Type7 and Type 8 are rectangular
how to Choose the right materials for medical cable manufacturing
Successful custom medical cable manufacturing requires careful attention to cable design, tooling, material selection, and processing methods. As a professional medical cable manufacturer, we have designed thousands of cables, overmolds, and assemblies for a wide range of applications, from the simplest to the most complex. Our expertise allows us to meet unique requirements, including those related to sterilization methods and other factors such as high flex cable and super low triboelectric noise.
When it comes to choosing the right materials for medical cables, both the jacket material and conductor material are critical. The jacket material must be carefully selected based on its compatibility with sterilization methods, while the conductor material is important for ensuring flexibility and optimal electronic properties. We understand the importance of using the correct materials for every application, and we work closely with our clients to identify the best options for their specific needs.
With our deep understanding of medical cable manufacturing and our commitment to quality, we are the ideal partner for any custom cable project. Contact us today to learn more about our capabilities and how we can help you achieve success.
Suitable Sterrilization Methods List Based On Different Materials
Conductor &Insluation & Jacket Material used in medical cable manufacturing
As a professional medical cable manufacturer, we understand the importance of carefully selecting conductor, insulation, and jacket materials in the medical cable manufacturing process. The choice of materials plays a crucial role in determining a cable’s performance, safety, and compatibility with different sterilization methods. Our expertise in material selection enables us to offer customized solutions that meet our clients’ exact requirements, while also delivering superior quality and reliability in every cable we manufacture.
Need more instruction? here is more guide | ||||
---|---|---|---|---|
Conductor Options | Shielding Options | Enhancement Options | Insulation & Jacketing Materials | |
Bare Copper | Bare Copper Braid | Strength Members | CPE/Chlorinated Polyethylene | PFA/Perfluoroalkoxy |
Tinned Copper | Tinned Copper Braid | Water Blocking | EPDM/Ethylene Propylene Diene Monomer | PFE/Perfluoroelastomer |
Silver Plated Copper | Silver Plated Copper Braid | Fillers | ETFE/Ethylene Tetrafluroroethylene | PP/Polypropylene |
Nickel Plated Copper | Nickel Plated Copper Braid | Rods | FEP/Fluorinated Ethylene | PTFE/Polytetrafluoroethylene |
High Strength Alloys | High Strength Alloys Braid | Tubes | Foamed FEP | PUR/Polyurethane |
Copper Clad Steel | Copper Clad Steel Braid | Foamed PFA | PVC/Polyvinyl Chloride | |
Prebonded Conductor | Stainless Steel Braid | Foamed PE | Silicone | |
Overcoated Conductor | Aluminum Mylar Foil Shield | Foamed TPE | Tefzel | |
Topcoated Conductor | Spiral Shield | Halar | TFE/Tetrafluoroethylene | |
HDPE & LDPE | TPE/Thermoplastic Elastomer | |||
Hytrel | TPR/Thermoplastic Rubber | |||
mPPE/Modified Polyphenylene | XLPE/Cross-Linked Polyethylene | |||
Neoprene | XLPO/Cross-Linked Polyolefin | |||
PE/Polyethylene |
Our Advantage In custom medical cable manufacturing
In-house Control
From cable design, conductor stranding, Shielding/coating and extruding to all types of sample testing, YQF keeps all steps of production in-house. Our vertically integrated approach means we have absolute control over quality, ensuring that the end product meets our strict standards and customers. It also means we can react quickly to customer demands and maintain aggressive production schedules while keeping costs at a competitive level
Flexible
World-Class Manufacturing Facilities Quick-Turn Prototyping Engineering Expertise High Mix, Low-Medium Volume Global Supply Chain Customer Service Flexibility Vertical Integration Ensures High Quality and Lower Costs
custom medical cable & Wire Free Design service
When it comes to medical devices, custom medical cables are often the best option for both medical cable manufacturers and medical device manufacturers. With the rapid development of medical technologies, companies are increasingly looking for ways to distinguish themselves from competitors and improve compatibility.
Medical cables can be thought of as the “nerves” of medical devices – they must be carefully selected to ensure optimal performance and reliability. A high-quality medical cable must meet basic requirements such as biocompatibility, suitability for a variety of chemical or physical sterilization methods, and long-term durability.
In addition, each medical device has unique requirements for physical performance, such as electronic properties, resistance, low-noise performance, data transmission performance/high frequency, and flexibility. To meet these diverse needs, it is essential to select the most appropriate conductor, insulation, shielding, jacket materials, and processing methods.
At our company, we specialize in designing and manufacturing custom medical cables tailored to the specific needs of our clients. We carefully analyze the device being outfitted with the cable, the frequency and type of sterilization methods used, and the extent of patient contact with the cable. With our expertise and commitment to quality, we deliver superior solutions that meet or exceed expectations.
3 Key Factors To Consider when Choose-Custom Medical Cable Manufacturer
To choose a reliable custom medical cable manufacturer is critical to a medical device manufacturer. When you are making a choice, there are 3 factors you have to consider:
First,Are they an experienced medical cable manufacturer?
Working with a experienced medical cable expert is critical if you want to keep your medical devices running safely, functionally and durable. A medical cable manufacturer must be ISO 13485 certified. This is the most direct way you can make a rough judgment how many years they have engaged in medical
cable. But this is not totally reliable, some cable manufacturers would like to apply all types of certifications when then founded the company.
An experienced medical cable factory
usually will ask you following questions when you make an inquiry if you did not give them your exact requirement:
- What medical device will the medical cable be applied to/used for?
- What is the acceptable OD(out diameter)and tolerance of the cable
- What is the gauge of each wire? Or how many strands of specific conductor you would like each wire to be
- Where is the medical device being used (i.e. X-ray room, doctor’s office, Ambulance, operating room, etc.)?
- Do you prefer disposable medical cable or reusable cable?
- What are your sterilization methods (chemicals or physical? What are the chemical sterilization materials? What is the
temperature, pressure, Ray (Ultraviolet, note: X-ray not used for sterilization)? - Will the medical cable be exposed to any other chemicals or fluids? Will there be any extra coat to protect the cable?
- What is the contacting level between the cable and patient (i.e. absolutely no contact, occasional contact, always
contact, implanted, etc. This relates to biocompatibility and material choosing)? - Do you have any supplementary requirements (such as, UL94 Level/framing rate, temperature resistant,ultra-flexible, Matt or Glossy, coiling etc.)?
Second:what are their producing equipment and laboratory testing devices?
Medical cable manufacturing has much more processing procedures than normal cable. And in most situation, it demands the conductors to be as thin as possible. For the
same gauge cable, thinner conductor will make it more flexible and better electronic performance. Not all conductor stranding machine can strand thin conductors as they are easy to break.so the precision level can determine the quality of the wire in some way besides of staff expertise. For testing devices, without the right testing devices, you cannot make related testing, such as RoHS,High Frequency,Triboelectric noise ,Tensile…(please refer to our Lab)
Third:Strategic Partners
For most industries, Partners belongs to commercial secret. For medical cable field, medical devices manufactures has a AVL(approved vendor list),similar to UL in some way. If a medical cable manufacturer is in the AVL of many worldwide famous brands,this is the easiest way for you to choose it as your potential partner too. YQF has be a partner for many famous brands and in their AVL for many years,contact us for trading reference if you are making medical cable supplier.